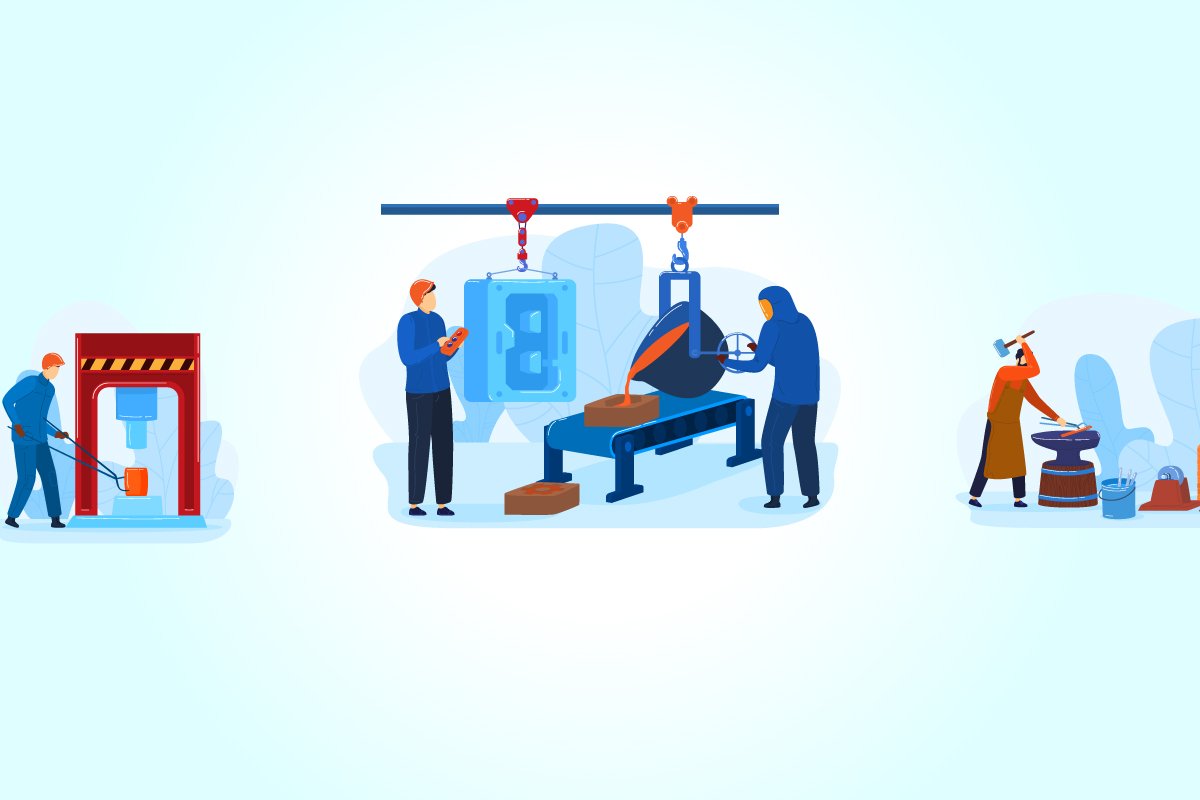
OEMs or ODMs are responsible to deliver quality components or products to the purchasing companies. To reduce the complaints from their clients OEMs or ODMs have to monitor each equipment manufacturing process. They not only have to monitor each process but also have to take some important decisions like choosing the correct process, choosing metal quality for the components, timely delivery from foundries, etc. OEMs have to work with the best alloy casting companies which have capabilities to deliver components on time and with perfect finishing. Especially, industries like food processing, oil and gas, marine and general engineering industries need to have commercial grade quality parts with precision and accuracy.
Just converting from one manufacturing process to another can be helpful to create quality components. To understand this let’s discuss converting your components/part manufacturing from sand casting process and forging process to investment casting process.
Convert from sand casting process to investment casting process:
If your casting supplier uses a sand casting process to make parts of the equipment then it’s time to consider changing to the investment casting process. It is a myth that the sand casting process is less time consuming than the investment casting process. Sand casting, eventually might result in the same lead time as it will require more machining and which will add cost and time to the overall process. Now, with the latest technologies and expertise companies like Austin Alloy Cast can process quality components in less turnaround time. Advanced lab testing facilities, skilled workers, robust infrastructure and global sales agent network are strengths of Austin Alloy Cast Pvt. Ltd.
Convert from forging to investment casting process:
The latest machinery and equipment used in any industry today are made to use components which are complex in design. To achieve the dimensional accuracy in the components with complex design, one must opt for advanced manufacturing processes like investment casting. The forging process has a limitation when manufacturing complex geometry components. We have helped numerous customers willing to change their forged component to an Investment casting component. Below is an example of it:
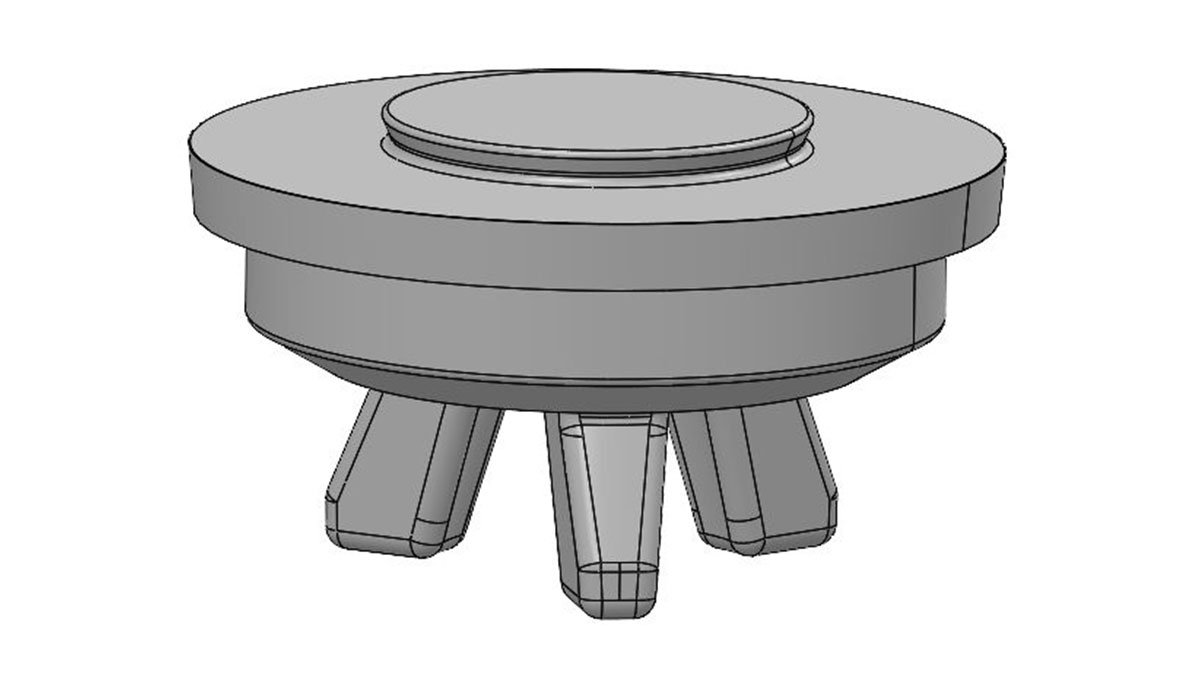
This Investment casting component is used in the Oil & Gas Industry.
Secondly, a mixture of alloys are used today to manufacture parts of machinery or equipment for various reasons. Alloy versatility is much greater in the Investment casting process than the forging process. The limitation of alloy sections with forging might be restrictive for developing quality components. However, when you want to develop any parts with alloys ranging from Carbon Steel, Low Alloy Steel, Stainless Steel, Nickel based alloys and Cobalt based alloys, Highly experienced Team at Austin Alloy Cast can handle a wide range of Steel alloys with utmost ease in the investment casting process.